When laying out assembly lines, every detail is considered. However, pressure on margins can lead production planners to neglect supposedly insignificant processes such as the lubrication of components or assemblies. The reason for this is a lack of knowledge or the wrong assumption that lubrication solutions are too expensive. A lubrication solution pays for itself within a short period of time: the greater the output, the faster the investment costs are covered.
Lean lubrication processes
In the age of Industry 4.0, the traceability of products is becoming more and more important. Applying grease with a brush is not only laborious and time-consuming, it also puts a stone in the way of optimising efforts. Because useful information is lost in the process. The clever assembly manager therefore asks himself:
- Is too much of the (possibly expensive) grease applied?
- Could unwanted residues or dirt particles get into the grease that is standing around in open containers?
- Will the grease also be applied to places where it is undesirable – such as adhesive points – and will it have to be removed again?
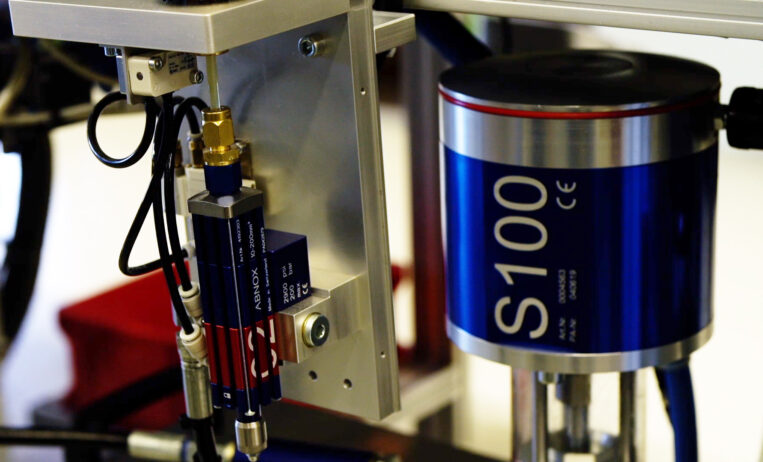
Investment in the future
With professional lubrication solutions, assembly lines expel products faster, more safely and in higher quality. Manual or semi-automated dosing systems apply the grease precisely and repeatably over thousands of cycles. Professional lubrication stations also contribute to a clean working environment, which automatically increases the motivation and efficiency of employees. Who feels good with constantly greasy hands?
By the way, the “retraction effect” of the ABNOX dosing valves also ensures impeccable cleanliness. This prevents the medium from dripping after the dosing process.
- Reduced throughput times / lean management
- Higher process reliability / higher product quality
- More cleanliness / greater employee motivation
- Eliminated waste of grease / minimised lubricant costs
- Flexibility / different lubrication cases per station
- Scalability / systems that can be easily retrofitted
A lubrication system should be designed in coordination with the other assembly processes. This is why far-sighted planners identify possible material flow bottlenecks that could arise from manual lubrication processes as early as the development stage of an assembly line.
Plug’n’Play thanks to the standard dosing device
Whether planned early or not, the new ABNOX standard Dosing Device AXDD is suitable for a large number of lubrication cases. The immediately available standard product is integrated into existing workstations surprisingly quickly. It is up to the customer whether he has his application nozzle developed by ABNOX or whether he manufactures it himself or whether he adapts one of the ABNOX standard nozzles.
Ultimately it means for the user: Connect the pump and compressed air, set the dosage and off you go!
Let experienced specialists design your own individual solution.
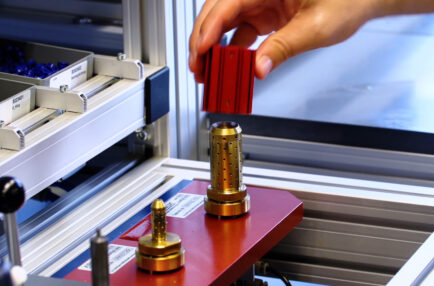