Toyota showed the world how to produce cars efficiently with the just in time principle in the 1970s. The criticism of decentralised production prompted by the corona crisis does not alter the continued relevance of the associated lean principle.
Lean management optimises business processes by eliminating waste and non-value-added activities. Furthermore, all processes that take place within a company are harmonised as far as possible in order to minimise downtime and waiting times. The philosophy encompasses principles of thought, organisation concepts and procedures that reduce complexity and improve the quality of products.
For example, metering valves and hand push pumps at ABNOX are assembled in a one-piece flow. Here the Swiss company employs the FIFO principle (first in, first out). A Kanban system is used to ensure continuous material availability. This guarantees shorter throughput times for standard products and improves process reliability. All workstations are also set up according to the 5S method and all in-house processes are subject to a continuous improvement process (CIP). The PDCA cycle (Plan, Do, Check, Act) is used for the ongoing verification of results.
More than the sum of all factors
In addition to structural factors however, lean management also encompasses social aspects such as the company culture. Benjamin Iseli, member of company management at ABNOX, explains: “With our flat hierarchies, we practice lean management from the bottom to the top.” Personal responsibility, teamwork and openness are demanded at all levels of the company. Strategic leadership, also known as lean leadership, encourages open information and feedback processes and error prevention activities. Not only does that help motivate the employees, it also improves the quality of all activities.
Lean principles are applied in many areas to this day, from lean thinking and lean development to the lean supply chain to lean administration or the lean laboratory. In other words, lean management is much more than the sum of all parts!
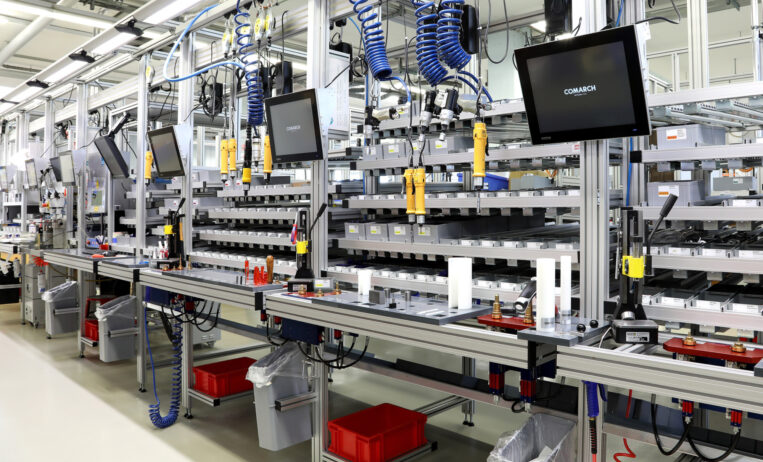
ABNOX streamlines your processes
The implementation of lean management needs to be all-embracing. A single bottleneck can slow down an entire assembly line. It is therefore obvious that the conveying and application of lubricants affects the overall productivity. If you also want to make sure that not a single excess gram of (costly) lubricating grease is applied, accurate dosing technology is essential.
ABNOX develops tailor-made system solutions while taking the existing resources and budget into account. From consulting to the layout to final testing, the experienced specialists optimise specific system solutions in close coordination with the customer.