If you want to minimise the consumption of expensive lubricants, you cannot avoid professional dosing technology. With the use of simple grease application solutions as well as more complex dosing systems, the investment costs pay off quickly - especially with volumetric systems. In comparison to the systems that dose according to time interval, the volumetric technology holds up even under changing environmental conditions. This is because it does not represent an uncertainty factor if the pressure or viscosity vary greatly due to fluctuating temperatures.
Stable and accurately repeatable
If you take it seriously, you can use a volumetric Metering Valves that is controlled on both sides instead of a simple, time-controlled Otlet Valves AXDV-A. Volumetric dosing processes ensure that the same volume of grease is applied over thousands of cycles. Both the start and the end position of the grease piston are recorded by means of sensors.
If the requirements are very high and air inclusions are not accepted, air bubble detection can help. Via a branch valve, the partial mass identified with it, which is found to contain air bubbles, is removed from the conveying system easily and without loss of time before reaching the dosing chamber.
ABNOX has a diverse range of standardised dosing valves, dosing devices and dosing valve stations in various sizes and designs:
- Standard Volumetric Metering Valves AXDV-C with mounting block or handle, which is also available as Volumetric Spray Valve AXDV-C-SPK
- Dosing Devices AXDD with integrated pneumatic control
- Metering Valve Stations for filling larger quantities
Three special applications
If, on the other hand, you always want to apply different amounts of grease, you can use Vario-Metering Valves AXDV-V. Instead of a conventional piston, an electrically driven worm shaft expels the grease. This enables fine adjustment and an immediate change in the amount of lubricant. The additional, practical advantage of these valves: The data supplied by the electric motor or the rotary encoder enable precise monitoring of the dosing process. No wonder these valves are in demand more and more.
ABNOX has developed the Rotary Dosing Unit AXDV-R1 for a further, very specific type of application. This combination of Vario metering valve and rotary unit hurls the grease evenly into a (mostly) cylindrical interior. The best-known example is probably the lubrication of the inner surface of an engine cylinder during the assembly process.
Finally, the Puls Valves AXDV-P, which dose quickly, accurately and contactlessly with up to 100 switching cycles per second, form a highly interesting category:
Have your desired dosing valve configured quickly and easily and discover how the various dosing valves work in this animation.
Our specialists are at your disposal for non-binding advice.
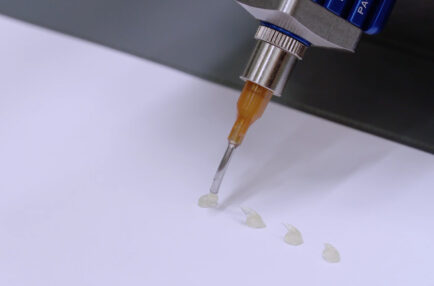