GF Rohrleitungssysteme supplies millions of high-quality manual and automatic industry and water distribution fittings each year. The corrosion-free plastic fittings are also used for the transportation of gases. Located in Seewis in the middle of the Swiss Alps, the plant in part has highly automated assembly lines. To stand up to worldwide competition, the global leader in fitting production consistently applies lean principles in its manufacturing operations.
Up to 75 per cent gain in efficiency
Toni Walser, Lean Champion at the GF site, recently replaced all manual lubricating instances with a specialised system from ABNOX: “We grease plastic fittings and the drives of assembly aids with the solution developed specifically for our needs.” This extends the service life of fittings that are subject to high stresses.
The cycle times for the individual lubricating instances were significantly reduced thanks to the new lubricating system. A complex instance for example was reduced from 20 seconds to 5 seconds. Thanks to exact application with repeat accuracy, GF was also able to minimise the consumption of costly lubricants. Another advantage: the standard ABNOX components require little maintenance and, as a configured system, do not cause any extra costs.
The ABNOX specialists designed a simple, expedient system according to Toni Walser’s requirements within a few months. A plug-and-play solution consisting of ten dosing units with a central grease supply was installed. The application focuses on process efficiency.
Tailor-made complete solution
The standard Dosing Device AXDD with integrated individual metering valve control are installed at five assembly stations. One of these units, which can be easily integrated into existing workstations, is equipped with a customer-specific quick-change system that permits the immediate exchange of lubrication fixtures. A central Drum Pump AXFP3-S supplies the grease, ensuring reliable lubricating grease conveyance and process stability.
The staff is elated by the investment with an amortisation period of just seven months. Now the employees no longer have contact with sticky lubricating grease and only need to remove grease residues from far fewer components. Contaminants in the lubricating grease have been considerably reduced as well. Toni Walser sums it up: “Thanks to the lean-compliant lubricating processes, we have not only eliminated various bottlenecks in assembly but also improved the quality of our fittings!”
Considering an individual lubricating solution? Our experts with many years of experience look forward to advising you with no commitment on your part!
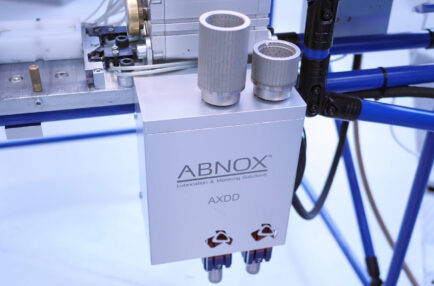