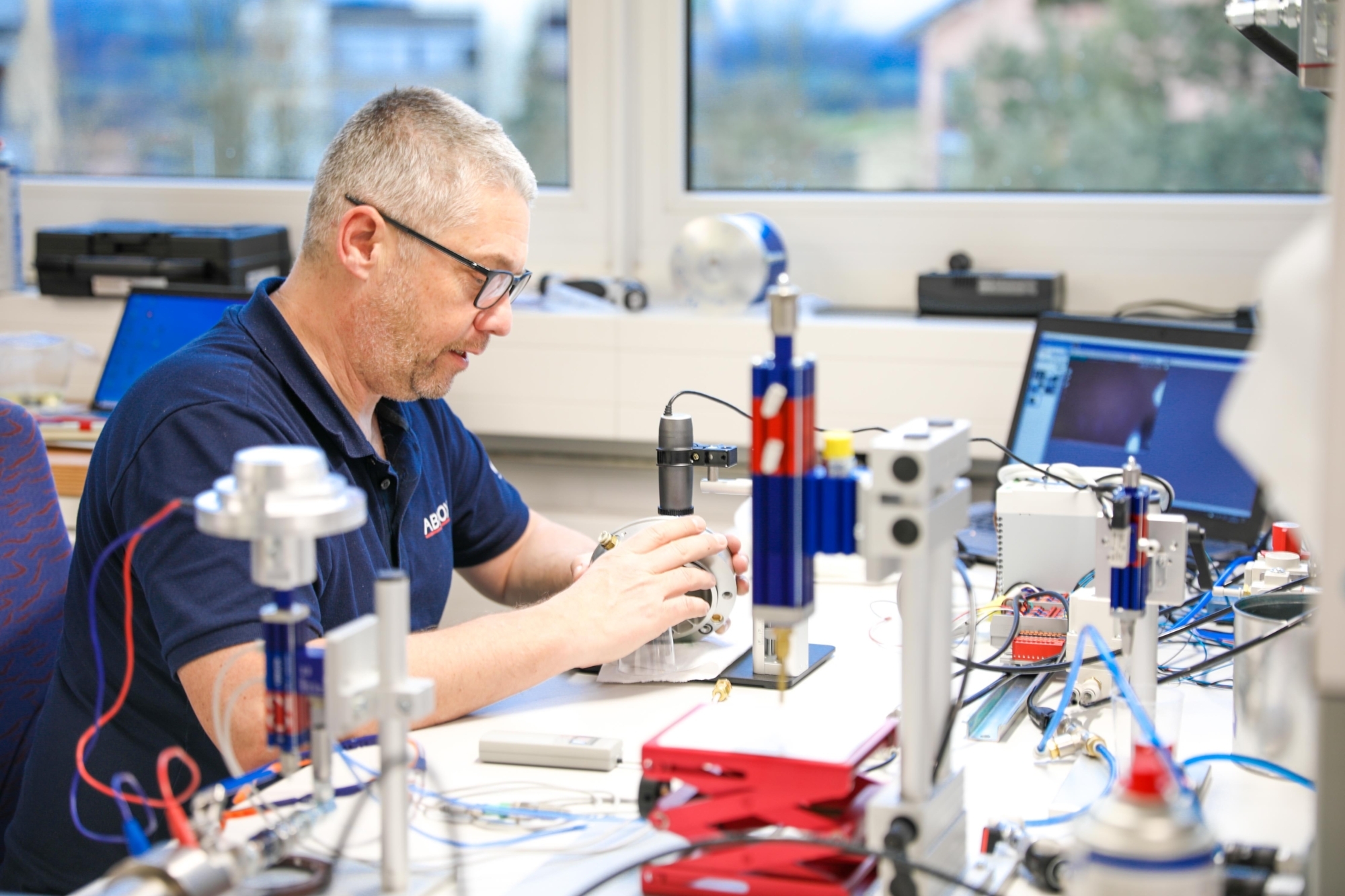
Frequently asked questions about ABNOX and our products
Delivering of lubricants
The delivering of lubricant is influenced by many different factors.
- One of the most important ones is the penetration (consistency). The higher the penetration NLGI-Class the stiffer the lubricant. Generally spoken: stiffer lubricant (grease) can not be pumped that easily. NLGI-Class 000 is the lowest class, i.e. the softest lubricant, NLGI-Class 6 is the stiffest, viscousest lubricant.
- Lubricants up to NLGI-Class 2 can be normally therefore the pumped without any problems.
- Most of the used lubricants correspond with the NLGI-Class 2.
- NLGI - Class = Rating of the lubricants, which is done by the National Lubricating Grease Institute.
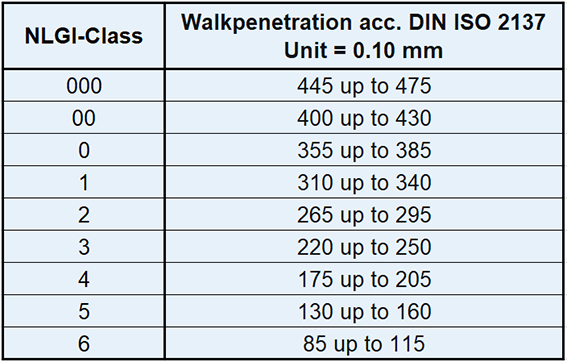
- The apparent dynamical viscosity, which is provided by certain manufacturers of lubricants, has an important meaning. If it goes beyond 5000 m Pa.s, pumping with conventional lubricant pumps or systems is complicated or not even possible.
- At the same time the surrounding temperature as well as the length of the conduits or hoses is also important.
- Synthetic or Bio-lubricants can affect the seal materials.
- If the solid content parts in the lubricant are too big, the pumping of such lubricant can be impossible with a conventional pump.
- Do not confuse silicone grease with silicone used for sealing (no lubricant).
The dependence of the delivery rate / lubricant container
Manufacturers deliver greases and lubricants in the most different containers and tanks. There is no standarized dimension or norm of the containers.
While pumping with pneumatic or electric pumps, the dimensions or the form of the containers have a certain importance for the right dimensions of the piston follower plate.
Conical containers or containers with large grooves can badly influence the pumping. Only special grease supply systems (Drum Pumps) should pump high viscositiy lubricants out of such containers.
The lubricant shouldn't be poured into another container. If really necessary, special criterions have to be followed. Air inlets and dirt can influence the quality of the pumping (consult the lubricant manufacturer).
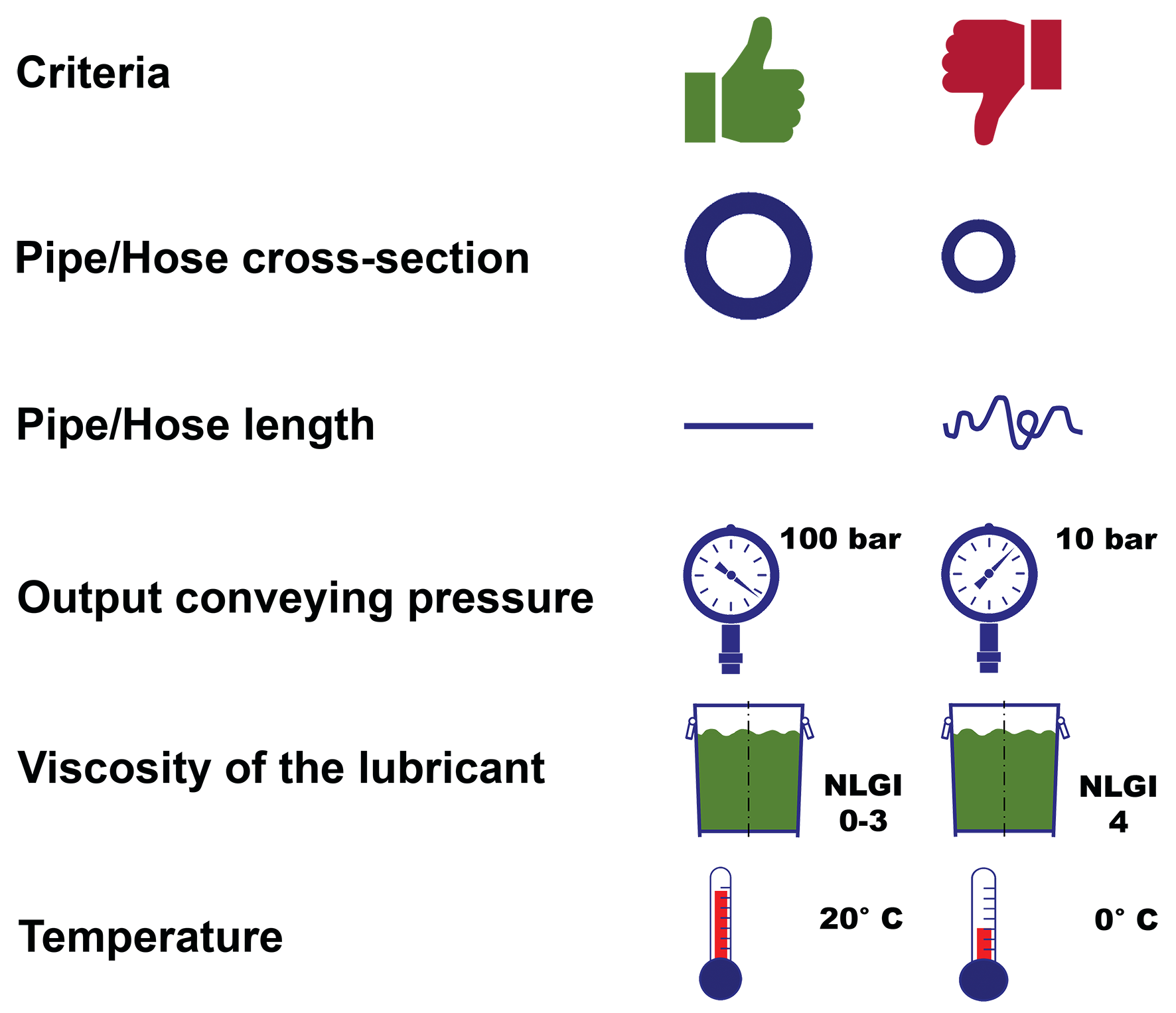
Please give attention!
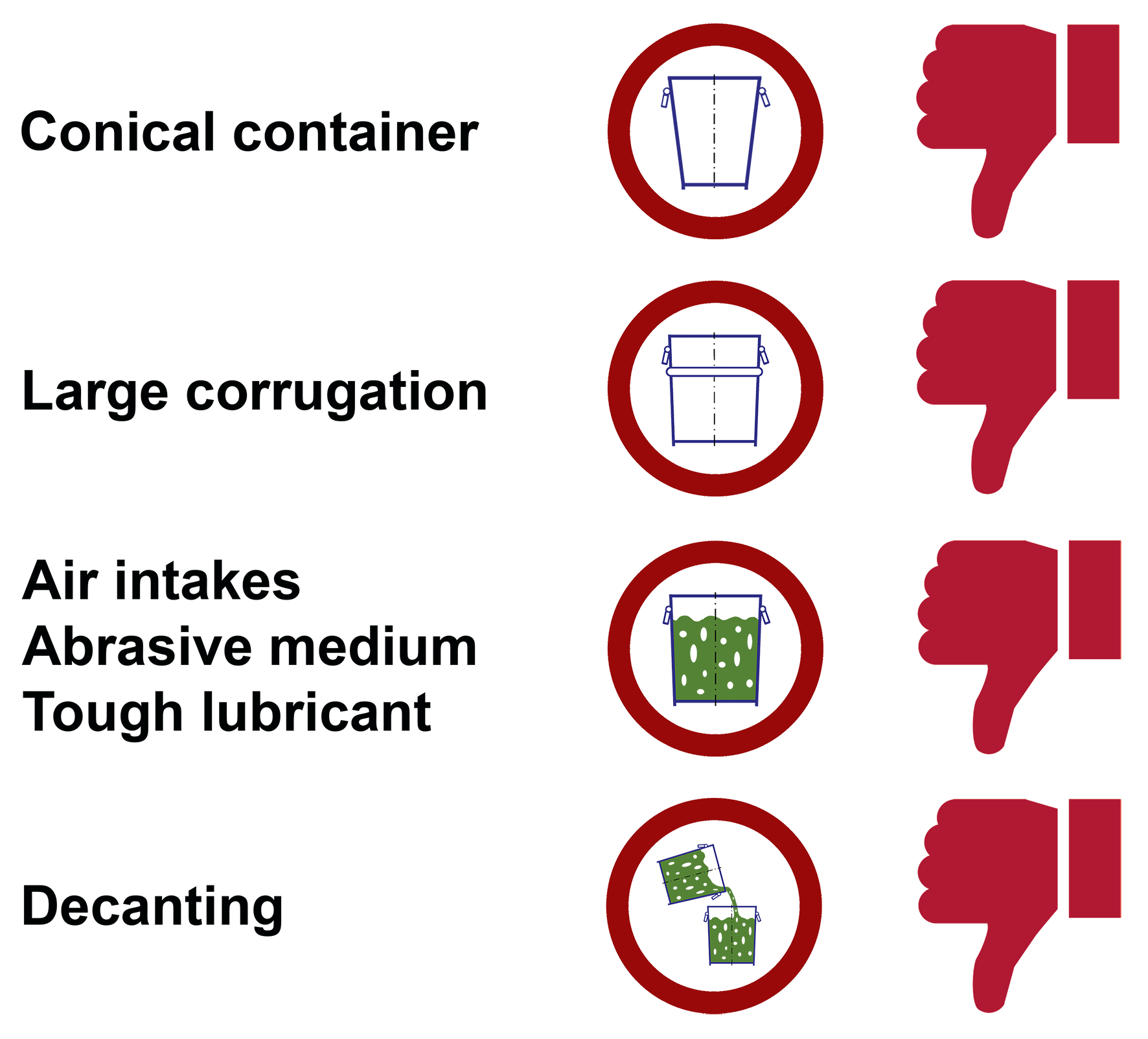
The right choice of the pump is important to achieve the success
Applications of ABNOX Grease Supply System
The wide range of lubricants-reaching from high viscosity grease to thin fluid oil-implicates the wide variety needs for lubricant supply pumps.
Standard pumps, commonly available for hydraulic applications, may be used for oil. In contrast, the properties of lubrication grease do not comply to Newton’s law, and in fact, high performance suction pumps may be required to handle some greases.
The most common solution for optimal and economic transferring of high viscosity lubricants (of class NLGI 1 to 3) is the use of the well-known air-operated piston pump.
Pressures of 50 to 150 bar are not uncommon if long transport pipes are used. Piston pumps are well capable to generate such pressure.
It is important to select the appropriate type of grease pump, with the appropriate suction, and the right grease supply system, which depends on equipment parameters such as pressure, feed quantity, temperature, viscosity and penetration properties of lubricants as well as the application.
ABNOX Grease Supply Systems are available for a range of different sizes grease containers and for a variety of applications:
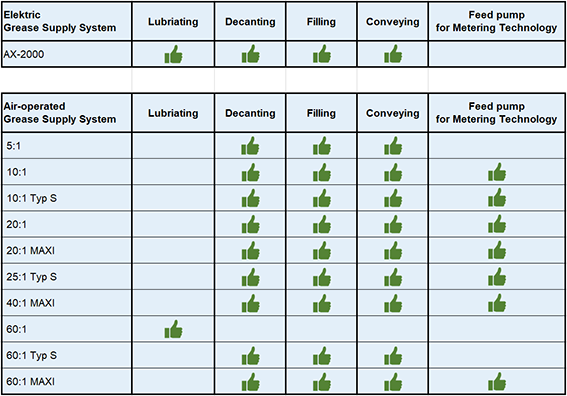
Reliable pumps with modern technologies
The Air-operated Grease Supply Systems of ABNOX operate with 2 up to 10 bar compressed air depending on the desired pressure ratio. The cylinder of the pump will automatically be switched before reaching the end position which generates the upward and downward stroke necessary for delivering.
This precise, mechanical switch-over is integrated inside the pump head and therefore well protected against external influences and manipulation.
The well-engineered geometric form of the valve and the sleeve with spring supported toggle guarantee a safe switching.
Air-operated lubrication pump V2010 / Sectional view air motor
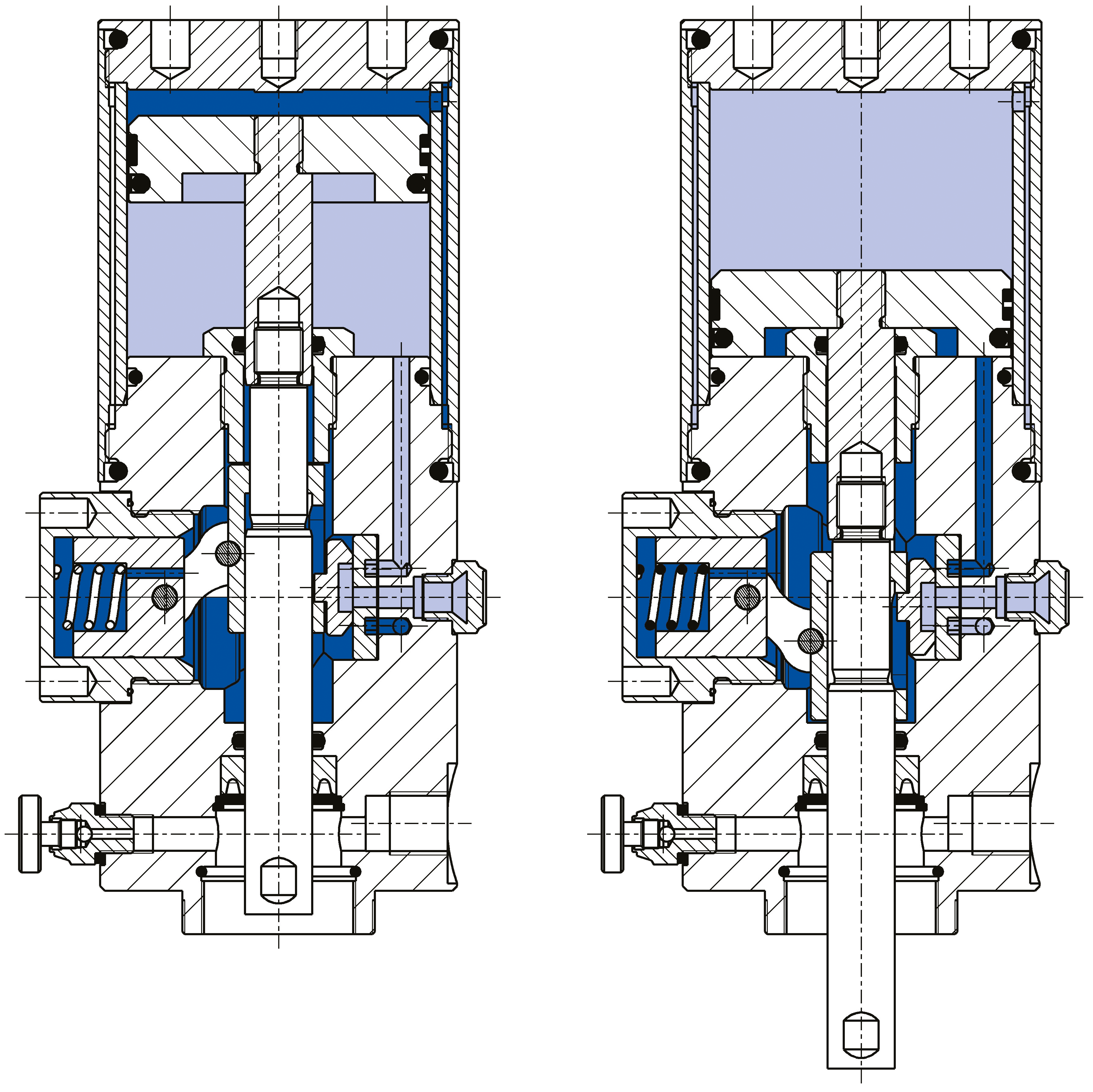
Suction system pressure ratio 5:1 / 10:1

Suction system pressure ratio 20:1 / 60:1
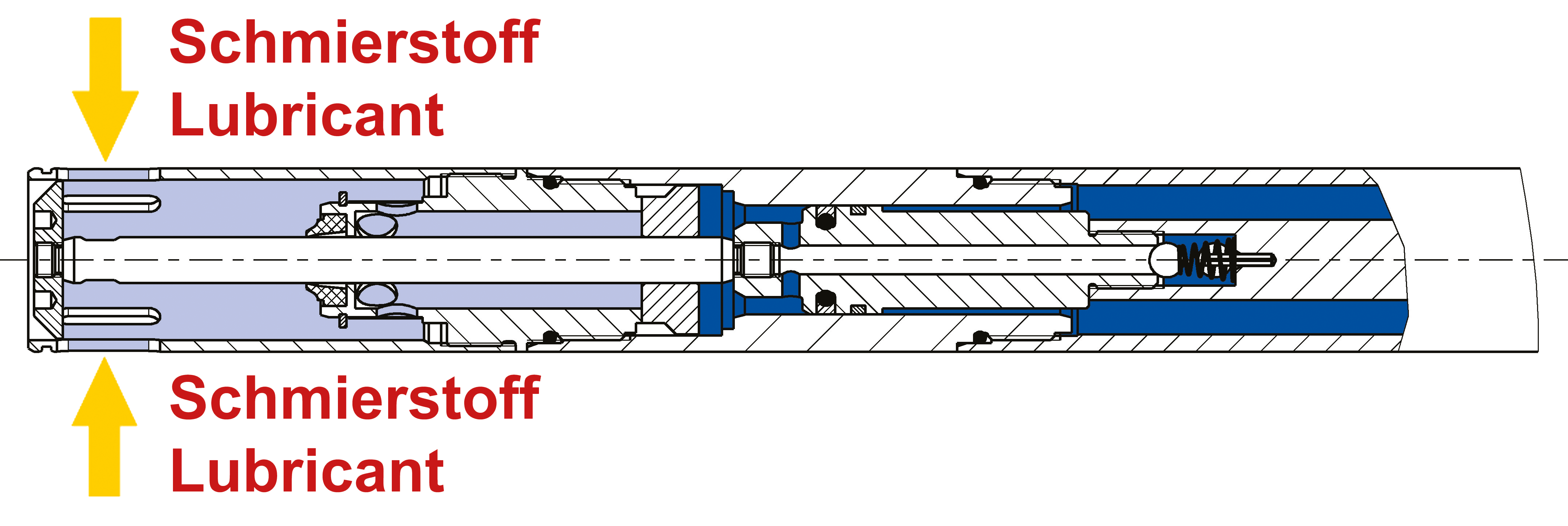
Air-operated lubrication pump AXSP
DELIVERY - METERING - APPLICATION - CONTROLLING
Reliable feeding, exact dosages and accurate dispensing mean clean, correct lubrication.
The call for maintenance-free operation, with no lubrication services needed, has become a standard request for equipment with moving parts. Lubrication is expected to last for a lifetime of the device. Apart from surface coating and special material match, lubrication materials are commonly used. Heavy duty lubricants are expensive, and high precision point exact metering is needed for their application. The key to minimize friction and wear, is to apply a lubricant with no maintenance needed in the right quantity and at the right place.
The nowadays used high performance lubricants have to be brought – according to the rules of tribology proper and carefully to the individual causes of friction. Correct lubrication means to bring the correct lubricant at the correct time in the correct amount to the correct place. For this purpose ABNOX delivers a range of products which allow implementing reliable feeding, exact metering and accurate dispensing.
The art of lubrication is accomplished in four steps:
DELIVERY
The wide range of lubricants reaching from high viscosity grease to thin fluid oil implicates the wide variety needs for lubricant supply pumps. Standard pumps, commonly available for hydraulic applications may be used for oil.
In contrast, the properties of lubrication grease do not comply to Newton’s law, and in fact, high performance suction pumps may be required to handle some greases. The most common solution for optimal and economic delivery of high viscosity lubricants (of class NLGI 1 to 3) is the use of the well-known pneumatic piston pump. Pressures of 50 to 150 bar are not uncommon if long transport pipes are used. Piston pumps are well capable to generate such pressure.
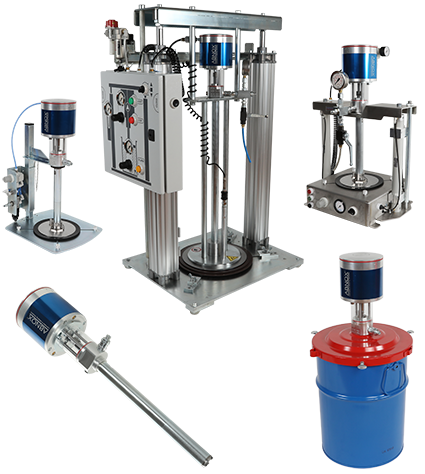
METERING
Grease and oil lubricants may be applied by various techniques.
For applications in the assembly processes, the use of time-controlled feed valves or volumetric metering valves have become widely accepted methods.
A main advantage of these valves is their simplicity and reliability.
A volumetric metering valve comprises an adjustable dosage chamber for the medium and an integrated pneumatic cylinder serving as an actuator.
The medium is conveyed to the metering valve directly from its original grease container, by a pneumatic piston pump.
The valve is controlled by means of a 5/2-way valve.
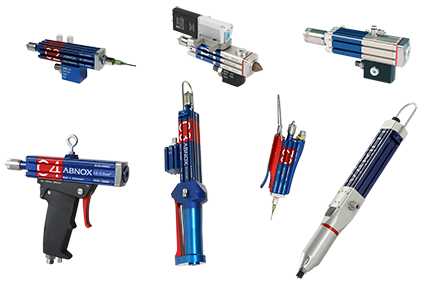
APPLICATION
Lubrication media must be applied in the right quantity at the right location.
The optimal approach is to place the lubricant directly into the area of friction.
To determine the best layout of the lubrication equipment, know-how and experience of the designer and the lubrication expert are required. The nozzle size chosen depends on the material properties and the target quantity of the lubricant.
E.g. excessive nozzle size causes inconsistent break-off of material flow, affecting metering precision.
A small nozzle leads to less back-flow after coating. Other questions need to be handled, such as the requested repeat accuracy, the allowed number of lubrication points served by one metering valve, the space requested for the working station, the operation cycle time and others.
Each lubrication task calls for individual analysis and for a specific solution.
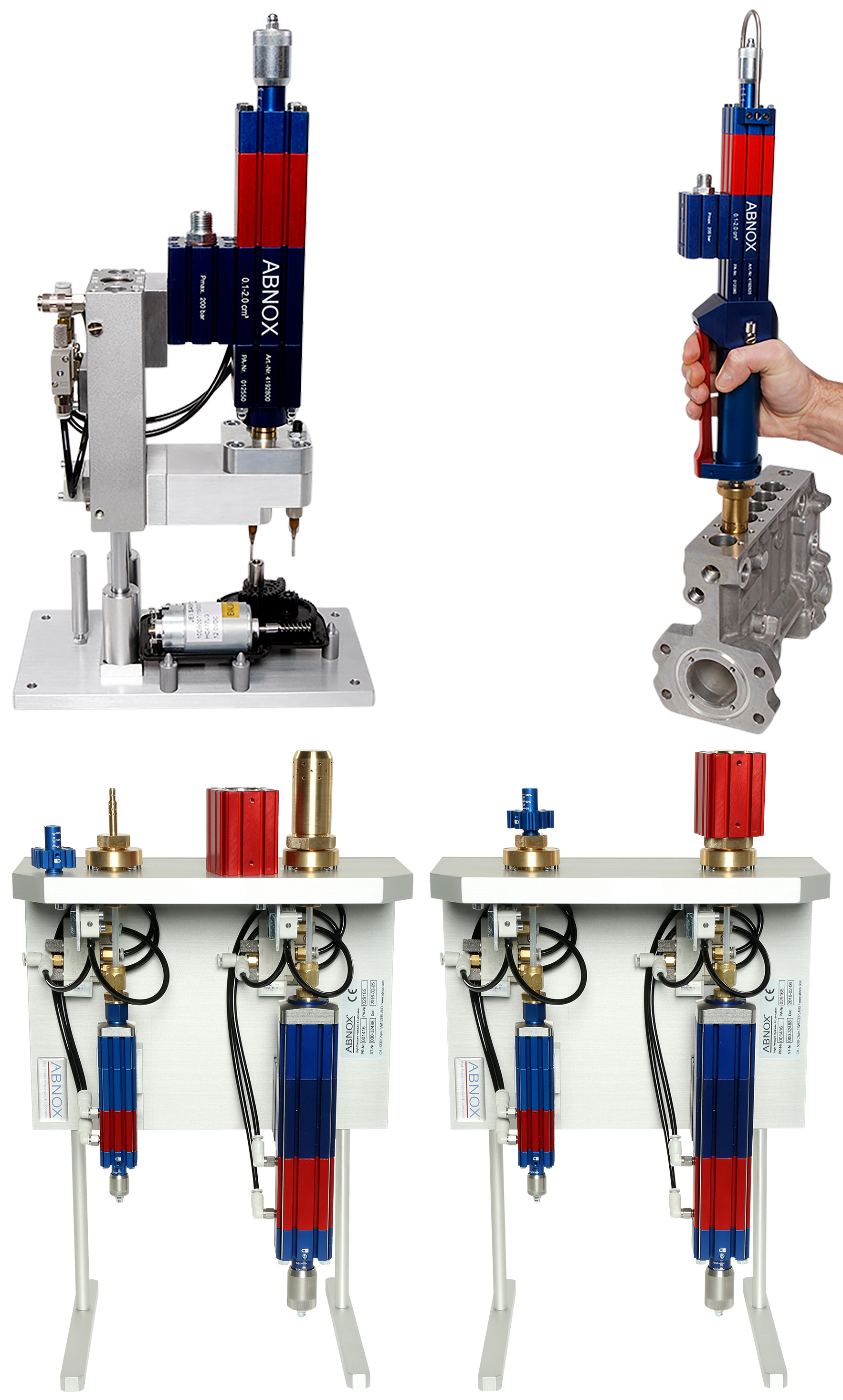
CONTROLLING
For lifetime lubrication of components, the correct lubrication quantity has to be applied to each friction spot with absolute certainty. Accordingly, the process monitoring support for the requested process reliability must conform to the highest standards.
Metering valves equipped with a position sensor are a low cost and hence frequently used approach to monitor the dosage process.
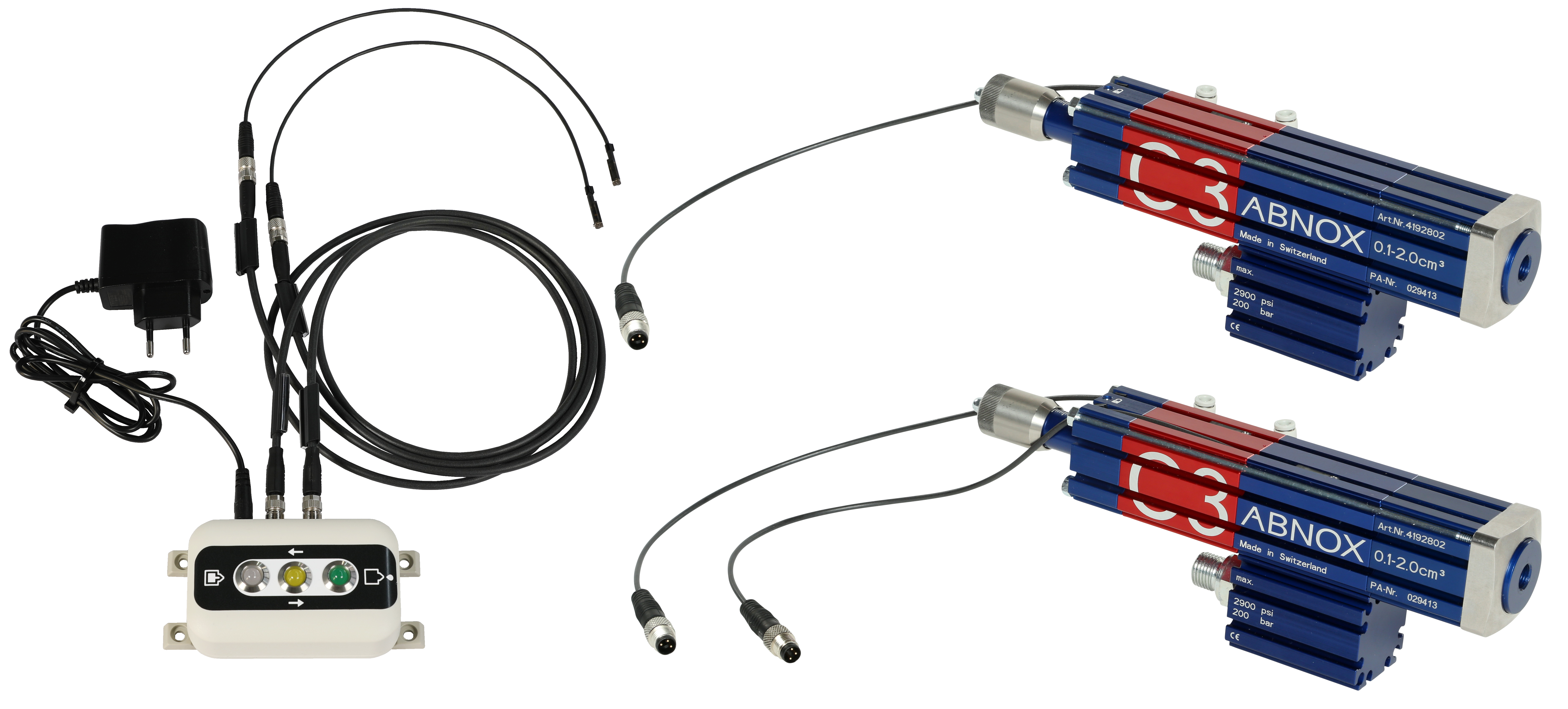
Animation ABNOX Dosing Device AXDD

The World of Metering Technology
Animation ABNOX Metering Valve AXDV-C

ABNOX Metering Valves provide the means for precise dosing using the latest developments in pressure control technology.
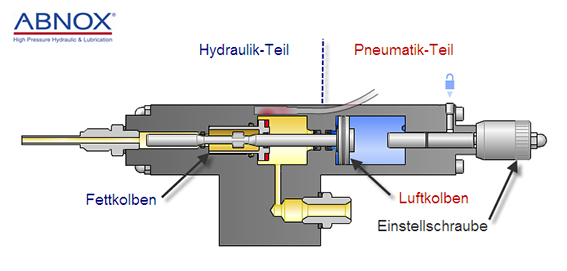
The skilful design of the Metering Valves guarantees the achievement of the right amount to the right place, at the right time. Greases of class NLGI 0 to 3 can be handled up to a maximum apparent viscosity of 5000 mPa.s. The Metering Valves can also be used with oils. This covers the majority of all applications. ABNOX Metering Valves can operate at any angle.
The dosage chamber inlet and outlet are alternatively shut and opened by means of a pin valve with pneumatic control. The dosage chamber volume is continuously adjustable by a lockable screw adjustment. The medium is ejected by means of the feeder pump pressure. The use of modern sealing components and glydrings ensures long lifetime of the metering valve even with high input pressures up to 200 bar and also when used with grease containing solid particles. A range of valves reaching from sizes 1 mm³ up to 500 cm³, allows to meet most lubrication technique requirements in an economic way.
Metering Valve with Sensor (control in the hydraulic part)
Metering piston is at the rear (no signal at sensor)
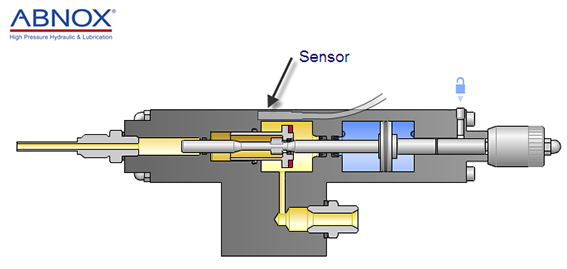
The position magnetic field sensor detects the motion (the end position) of the metering piston and, consequently, the ejection of the lubricant.
Metering piston at the front - end position (signal present at sensor)
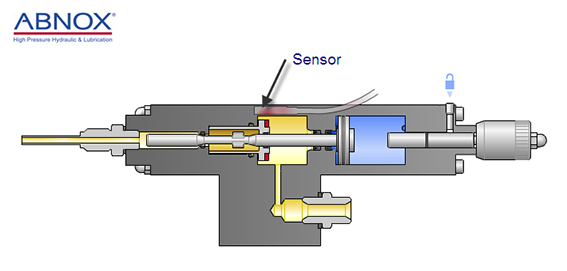
Its output signal confirms the completion of the lubricant transfer. A missing signal indicates lack of lubricant flow, or other failure.
This dosage sensor signal allows for a simple process monitoring. The rugged design ensures a high lifetime.
ABNOX Drum Pumps AXFP-Series, the right tool for efficient and reliable transferring lubricants with high viscosity levels.
Discover the functionality and simple operation thanks to a clear and understandable presentation of the new pump control.
Animation ABNOX Drump Pump AXFP

Commissioning of an ABNOX Drum Pump AXFP
ABNOX Can Pumps AXKP-Series, are the ideal and cost-effective systems for conveying expensive lubricants, including silicone greases and oils, from cartridges and small containers.
Watch our animation on how to commission an ABNOX air-operated can pump AXKP.
Animation ABNOX Can Pump AXKP
